Table of Contents
Water pumps are unsung heroes in our daily lives. They are crucial across numerous industries. From ensuring a steady water supply in our homes to playing a vital role in large-scale industrial and agricultural operations, these devices are everywhere. In this blog, we’ll take an in-depth look at water pumps, covering their types, working principles, applications, how to choose the right one, and common issues and solutions.
What is a Water Pump?
At its most basic, a water pump is a mechanical device designed to move water from one location to another. It uses mechanical or hydraulic principles to create the necessary force for water transfer. Water pumps have been around since early civilization in one form or another, and today, they are an essential part of housing, farming, municipal, and manufacturing sectors.
Working Principle of Water Pumps
Most water pumps operate on either the positive displacement principle or use kinetic energy to push water. They are powered by various sources, such as AC or DC electricity, gasoline engines, or diesel engines.
Positive Displacement Pumps
Positive displacement pumps work by mechanically contracting and expanding a flexible diaphragm to supply a set amount of water flow. These pumps are highly effective in industries that deal with high – viscosity fluids where sensitive solids may be present. They are ideal for applications that require a combination of high pressure and low flow. However, they need extremely little clearance between the revolving pump and the external edge of the unit, which means they must operate at very slow speeds. Running them at high speeds can lead to a decrease in efficiency.
Centrifugal Pumps
Centrifugal pumps are equipped with a rotating impeller. As the impeller spins, it creates centrifugal force, which pushes water outwards from the center of the pump towards its edges. This action creates a low – pressure area at the center, allowing water from the source to flow into the pump. The spinning impeller then accelerates the water, increasing its speed and pressure before it is pushed through the pump’s outlet.
Centrifugal pumps are suitable for pumping low – viscosity liquids and are commonly used in building water systems, well water supply, and for increasing water pressure in intake lines. However, they can face issues such as overheating due to low water supplies, cavitation (the formation of air bubbles near the impeller), and wear of the impeller from solids in the fluid.
Types of Water Pumps
Water pumps come in a wide variety of types. Each type is designed for specific applications. Here are some of the most common ones:
Submersible Pumps
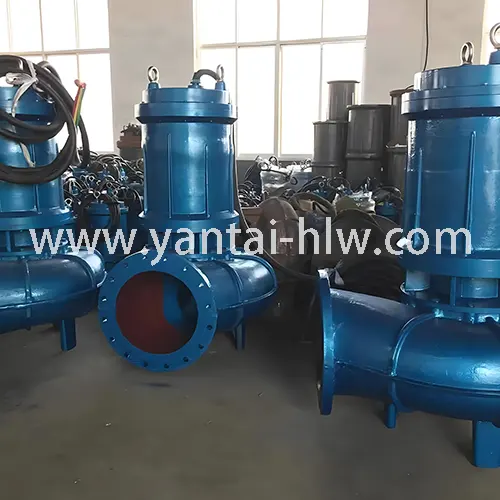
These pumps are designed to be completely submerged in water, whether it’s in a borewell or an open well. The motor of a submersible pump is sealed and made of corrosion – resistant materials to withstand prolonged submersion. Since they operate underwater, they eliminate the need for priming and prevent air from entering the system, ensuring a continuous water supply. Submersible pumps come in different sizes and power levels to meet the requirements of various water sources and depths. They are a popular and efficient choice for household water supply needs, especially in areas where the water source is underground.
Jet Pumps
Jet pumps are specifically designed to draw water from deep sources, such as bores or wells that are located much lower than the desired destination. Many jet pumps are electrically driven, but engine – driven models are also available. They work by using a jet of water or air to create a vacuum that draws water from the source up into the pump. Jet pumps are often used in rural or remote areas where access to a deep water source is necessary.
Diaphragm Pumps
Diaphragm pumps use a different mechanism compared to centrifugal pumps. They are designed to pump thick contents such as sewage, mud, or water with a high solid content. These pumps use a flexible diaphragm that is mechanically actuated to create a vacuum and pressure cycle, which draws in and then pushes out the fluid. Diaphragm pumps are suitable for applications where the fluid being pumped contains solids or is highly viscous.
Stationary Pumps
Stationary pumps are typically large – scale units used for industrial or agricultural purposes. They can be powered by electricity or diesel engines. These pumps are designed to move large quantities of water over long periods. In industrial settings, they may be used for processes such as cooling systems, while in agriculture, they can be used for large – scale irrigation. Stationary pumps are often a key component in maintaining the continuous operation of large – scale water – related systems.
Booster Pumps
As the name suggests, booster pumps are used to increase the pressure of water in a system. They are commonly used in households where the incoming water pressure is low, such as for showers, faucets, or appliances like washing machines. Booster pumps take the existing water pressure and intensify it before distributing the water throughout the house. They are also used in commercial and industrial settings where a higher water pressure is required for specific processes.
Applications of Water Pumps
Water pumps have a vast range of applications across different sectors:
Residential Applications
– Water Supply: In many homes, especially those relying on well water, water pumps are essential for getting water from the source (well) to the house. Submersible pumps and jet pumps are commonly used for this purpose.
– Irrigation: Sprinkler pumps are used to water lawns, gardens, or small – scale farmland. They ensure that plants receive an adequate water supply for healthy growth.
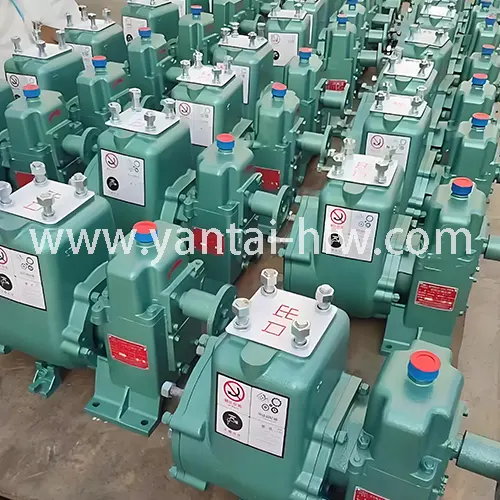
– Drainage: Sump pumps are used to remove water from basements or crawl spaces to prevent flooding. They are particularly important in areas with high water tables or during heavy rain events.
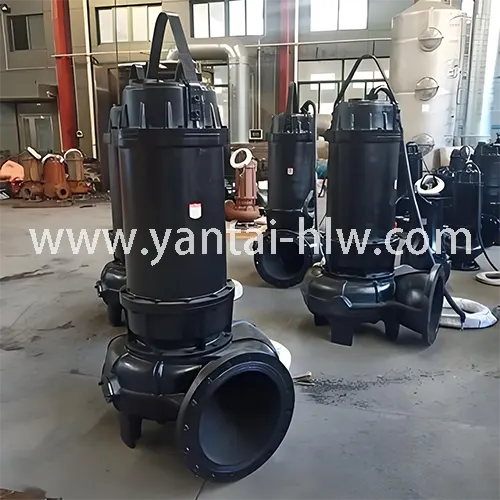
Industrial Applications
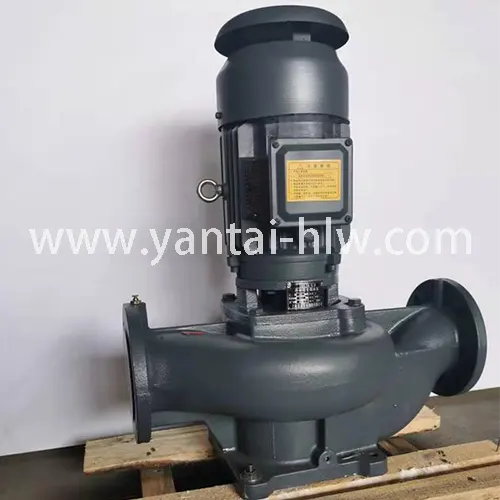
– Manufacturing Processes: Water pumps are used in various manufacturing industries. For example, in the food and beverage industry, they are used for transferring liquids, cleaning equipment, and cooling processes. In chemical manufacturing, pumps handle and transfer different chemicals.
– Power Generation: Cooling water pumps are crucial in power plants. They circulate water to cool the equipment and prevent overheating.
– Mining: In the mining industry, pumps are used for dewatering mines. This helps to keep the working areas dry and safe. They also transport minerals and slurries.
Agricultural Applications
– Irrigation: Large – scale agricultural irrigation systems rely on pumps to move water from sources such as rivers, lakes, or underground wells to the fields. This ensures that crops receive enough water throughout the growing season.
– Drainage: In areas with poor drainage or high water tables, pumps are used to drain excess water from the fields, preventing waterlogging, which can damage crops.
Municipal Applications
– Water Supply Systems: Water pumps are used to lift water from treatment plants to storage tanks and then distribute it to homes and businesses. Booster pumps are often used to maintain adequate water pressure in the distribution system.
– Sewage and Wastewater Treatment: Pumps transfer sewage from collection points to treatment plants. They also move wastewater through the various treatment processes.
How to Choose the Right Water Pump
Selecting the perfect water pump for your needs involves considering several factors:
Understanding these issues can help in effective troubleshooting and maintenance.
Application – Specific Requirements
The first step is to determine the intended use of the pump. Are you using it for residential water supply, industrial processes, agricultural irrigation, or something else? Different applications require different types of pumps. For example, if you need to pump water from a deep well to your home, a submersible or jet pump would be a suitable choice. If you are dealing with sewage or water containing solids, a diaphragm or trash pump might be more appropriate.
Flow Rate and Pressure
– Flow Rate: Measured in gallons per minute (GPM) or liters per minute (L/min), the flow rate indicates how much water the pump can move in a given time. For applications that require quick water transfer, such as draining a flooded basement, a pump with a high flow rate is necessary.
– Pressure: Water pressure is measured in pounds per square inch (psi). The required pressure depends on how far the water needs to be pumped vertically (total head lift) and horizontally. For example, if you need to pump water to a high – rise building, a pump with sufficient pressure to overcome the height is essential.
Power Source
Water pumps can be powered by various sources. These include electricity, gasoline, diesel, or even solar energy.
– Electric Pumps: These are great for indoor use and are often more energy – efficient. Most electric pumps can be plugged into a standard household outlet (120V), but some larger models may require a 230V outlet. However, they are limited by the need for an electrical source and may not be suitable for mobile applications.
– Gasoline and Diesel Pumps: These pumps are more powerful and are commonly used at job sites, farms, or in situations where a lot of water needs to be moved quickly. They are also suitable for outdoor use where access to electricity is limited. However, they produce carbon monoxide emissions and require regular maintenance, such as oil changes.
– Solar – Powered Pumps: In areas with abundant sunlight and limited access to electricity, solar – powered pumps are a sustainable option. They are often used for small – scale irrigation or water supply in remote locations.
Inlet and Outlet Sizes
The inlet and outlet sizes of the pump are important. The pump sucks in water through the inlet valve and ejects it from the discharge valve. A larger – sized inlet and outlet, for example, a 4 – inch dewatering pump compared to a 1 – inch pump, can potentially move water more quickly. It’s crucial to ensure that the size of the inlet hose matches the inlet size of the pump to prevent any reduction in water flow.
The material of the pump is crucial if it will be exposed to harsh conditions. For outdoor use or when pumping corrosive substances, pumps made of weather-resistant and corrosion-resistant materials, like stainless steel or certain plastics, are more suitable.
The material of the pump is especially important if it will be exposed to harsh conditions. For outdoor use or when pumping corrosive substances, pumps made of weather – resistant and corrosion – resistant materials, such as stainless steel or certain plastics, are more suitable. The durability of the pump will also depend on factors like the quality of the bearings, seals, and the overall construction.
Common Water Pump Problems and Solutions
Despite their importance, water pumps can encounter various problems over time. Here are some common issues:
Low Water Output
– Possible Causes:
– The suction pipe may not be tight, causing air intake, which results in milky – looking water with bubbles.
– The rotation direction of the pump may be wrong.
– The valve may not be fully opened.
– The pump speed may be insufficient, which could be due to low power supply voltage or incorrect speed settings.
– The pump head may be too low for the required application.
– The flow meter may be malfunctioning.
– There could be a foreign body blocking the suction pipe or the impeller flow path.
– Solutions:
– Check the suction pipe for leaks and plug them.
– Reverse the motor power wiring (switch any two of the three wires) if the rotation direction is wrong.
– Check and open the valve fully.
– Check the power supply voltage and, if it’s a speed – control pump, increase the speed.
– Replace the pump with one that has a higher head.
– Recalibrate, repair, or replace the flow meter.
– Stop the pump and disassemble it to remove any foreign bodies.
Pump Vibration and Noise
– Possible Causes:
– The fixing bolts of the motor and water pump feet may be loose.
– The pump and motor may not be concentric.
– Severe cavitation may be occurring in the pump.
– The bearing may be damaged.
– The pump shaft may be bent or worn.
– The water pump impeller or motor rotor may be imbalanced.
– There may be debris inside the pump.
– The coupling inner column bolt or rubber column may be worn or damaged.
– The flow may be too large or too small, outside the pump’s allowable operating point.
– Solutions:
– Readjust and tighten the loose bolts.
– Readjust the concentricity of the pump and motor.
– Reduce the water output, increase the water level of the suction tank or well, or replace the pump with one that has a higher vacuum if cavitation is the issue.
– Replace the bearing with a new one.
– Repair or replace the pump shaft.
– Disassemble the pump to check for imbalance and perform static and dynamic imbalance tests if necessary.
– Open the pump cover and remove any obstructions.
– Check and repair or replace the coupling inner column if needed.
– Adjust and control the water output or upgrade the equipment to match the actual working conditions.
Bearing Overheating
– Possible Causes:
– In a sliding bearing, the oil ring may rotate slowly with little oil or the oil level may be low.
– There may be insufficient cooling water supply in the fuel tank.
– Water in the fuel tank can destroy the lubricant film.
– The lubricant grade may not meet the original design requirements, or the oil may be dirty.
– The shaft and the inner ring of a rolling bearing may loosen, causing friction.
– Solutions:
– Check the oil level, observe the oil ring transmission speed, and repair or replace the oil ring if necessary.
– Check the cooling water pipe and its joints for blockages and remove them.
– Check the cooling water pipe and fuel tank seal, resolve any leaks, and replace the oil.
– Use the correct lubricating oil as per the instructions, regularly check the oil quality, and periodically replace the oil.
– Repair the shaft diameter or replace the pump shaft and bearing.
Heating in the Stuffing Room
– Possible Causes:
– The packing gland may be pressed too tightly.
– The sealed cooling water pipe section may not be opened or may be opened insufficiently.
– The packing may have been replaced improperly, causing the water seal to be displaced and blocking the water holes.
– There may be no water from the pump, resulting in no cooling water lubrication.
– Solutions:
– Adjust the packing gland bolts to the proper tightness.
– Open the cooling water pipe section fully and control the water in the stuffing room to drip continuously (ideally 30 – 60 drops per minute).
– Stop the pump and readjust the position of the water seal ring so that its water inlet aligns with the cooling water injection hole.
– Stop the machine and restart it according to the operating requirements.
Conclusion
Water pumps are incredibly versatile and important devices. By understanding their types, working principles, applications, how to choose the right one, and how to troubleshoot common problems, you can make the most of these essential tools, whether in your home, workplace, or agricultural fields.